Building a company worth working at
A safe and healthy working environment
We strive to create a safe and healthy working environment and promote health among employees working in the Haseko Group and employees of partner companies.
Toward the realization of a safe and healthy working environment
Policy for safety and health
At the Haseko Group, we establish a Group-wide “Basic Policy for Safety and Health Management” that stipulates a safety and health policy for Group employees each year, execute thoroughgoing initiatives to eliminate occupational accidents and work to create safe and comfortable workplaces on an ongoing basis.
Furthermore, construction sites of Haseko Corporation establish a safety and health policy and specific implementation measures including partner companies under the Safety and Health Management Plan each year. In order to minimize occupational accidents, not to mention reducing fatal and serious accidents/disasters to zero, we treat the elimination of factors that cause human errors as a priority issue in our activities.
Group Basic Policy for Safety and Health Management (Japanese Only) [PDF:174KB]
Haseko Corporation Safety and Health Management Plan (Japanese Only) [PDF:11MB]
*The Haseko Corporation Safety and Health Management Plan applies to Haseko Corporation’s construction sites and partner companies that undertake construction work.
Framework for promoting health and safety
Although the Haseko Group has not been accredited with Occupational Health and Safety Management Systems (OHSAS) 18001, it has voluntarily set up the Safety and Health Central Committee as a supervisory system in which directors oversee safety matters, chaired by the President and Representative Director of Haseko Corporation to administer the respective Safety and Health Committees. The Safety and Health Committee of each Group company also works on creating safe and comfortable workplaces on an ongoing basis, through concerted efforts made by members of the Committee and industrial doctors.
In fiscal 2022, with “Eliminate the occurrence of human error and aim for zero accidents and zero disasters” as our slogan, we executed thoroughgoing initiatives to eliminate occupational accidents at each business site, and committee members for safety and health promotion of each company continuously played a central role in creating a safe and comfortable workplace environment.
For elimination of occupational accidents, we conducted activities by setting the frequency rate of occupational accidents at 0.60% or less and the severity rate of occupational accidents at 0.01% or less as target figures for accidents (*) at construction sites, and we achieved these targets. For the creation of a safe and comfortable workplace environment, we further promoted non-working days together with workers in order to rectify long hours of work as part of Workstyle Reform at construction sites. We also made Group-wide efforts in this area at the organization level in collaboration with MOSt Activities.
*Target for occupational accidents resulting in four or more days of absence from work at Haseko Corporation
At meetings of the “Safety and Health Central Committee,” the President and Representative Director of Haseko Corporation, who chairs the committee, and the committee members, comprising the officers in charge of each department and the presidents of each Group company, as well as the representatives of the labor union of the Haseko Group, participate in deliberations and discussions regarding safety and health. At the Safety and Health Committees of Group companies, members nominated by the labor union of the Haseko Group and those who represent a majority of the employees.
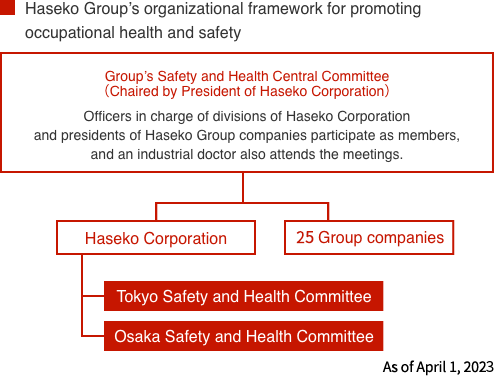
Activities to raise safety awareness
To eliminate occupational accidents, it is essential that each and every employee act in his/her day-to-day work with safety in mind.
In addition to proactive utilization of posters and bulletin boards to help raise employees’ awareness, we conduct risk assessment through regular safety patrolling at the Group’s construction sites where everything takes place to ensure safety management.
Regarding safety and health education for its own employees, Haseko Corporation implements training each fiscal year on matters such as the basic points of laws, regulations, and rules related to safety and health, the key points in managing each type of construction work, accident case studies, etc. as part of practical training for each year level and position from young to mid-level employees in the construction divisions. Employees who have worked at the Company for a certain number of years and who are in certain positions must participate in this training.
We also implement safety and health education for cooperating companies engaged in construction work together with us. Specifically, in addition to training for foreman-level workers and those responsible for safety and health at cooperating companies, we also hold on-site training concerning the handling of equipment and machinery used in construction work and how to use equipment to prevent accidents. An aggregate total of 1,897 employees of cooperating companies participated in this training in fiscal 2021.
In addition, we also have implemented safety and health education for cooperating companies engaged in construction work as partners. Specifically, we have provided training targeted at foreman and personnel responsible for safety and health in these companies.
“Experiential safety VR training” using virtual reality (VR) devices was introduced as one of hands-on trainings for cooperating companies in December 2021. By allowing participants to simulate the experience of occupational accidents through realistic VR scenes, we aim to raise their safety awareness.
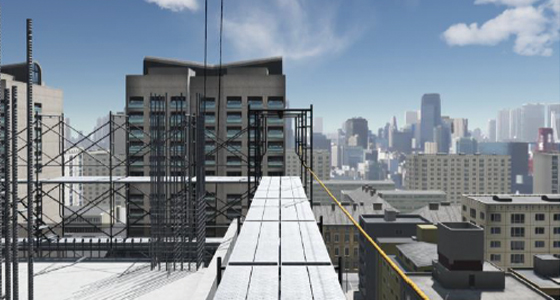
(experience of falling from temporary scaffolding)
Ensuring safety on construction sites
Before beginning work on new construction projects, Haseko Corporation holds meetings of the Construction Plan Examination Committee aimed at ensuring appropriate and smooth construction. In addition to the Construction Dept. and site foreman responsible for managing the construction site, the Safety Management Dept., the Technical Support Dept., and the Environmental Systems Dept. also participate in committee meetings. They examine the various risks associated with each project and provide guidance and advice to the Construction Dept. and site foreman. Likewise, in terms of safety management, we evaluate risk based on the unique circumstances of each project and implement suitable countermeasures to ensure safe construction work.
After construction work commences, we implement “worksite safety and health patrols,” where employees in the Safety Management Dept. visit all construction sites. Employees carrying out these patrols inspect the status of each site’s safety and health management, the completeness of relevant documentation, etc. based on a checklist, and provide necessary guidance on improvements. The results of these inspections are shared with the Construction Dept. responsposteible for managing the construction site and the officer in charge of the construction divisions. The Internal Auditing Department also audits each form of management implemented by the Safety Management Dept. through its internal audits.
The scope of audits by the Internal Auditing Dept. is not limited to construction sites and includes the status of management related to industrial safety and health, such as audits of the status of working hours management across all divisions, including Group companies.
Status of occupational accidents and action taken in response
In fiscal 2022, we set a goal of zero fatal and serious accidents/disasters and there were no fatal and serious accidents. We have established a system in which, in the event of an accident, we investigate the cause of the accident, formulate preventive measures, and work to prevent recurrence.
For example, if even the slightest accident occurs at a construction site, Haseko Corporation’s construction divisions attend to injured personnel and restore the construction site, while raising awareness at other construction sites and, mainly through the Safety Management Dept., confirms the background and cause of the accident and implements measures to prevent recurrence based on the results of this confirmation.
We not only analyze the causes of individual accidents but also analyze all the accidents that occur over a period of time, including factors such as the type of accident, the type of construction work, the day of the week, the time of day of the accident, and the age and years of experience of those involved, to prevent any recurrence.
In addition, we endeavor to strengthen our accident prevention framework across the entire Group by sharing accident case studies and information on measures to prevent any recurrence, not only within Haseko Corporation but also with Group companies engaged in construction work.
Safety performance
This table can be scrolled
(Fiscal year) | 2018 | 2019 | 2020 | 2021 | 2022 | |
---|---|---|---|---|---|---|
Frequency rate | Four work-days lost or more | 0.34 | 0.35 | 0.52 | 0.22 | 0.28 |
One work-day lost or more | 0.56 | 0.63 | 0.72 | 0.45 | 0.53 | |
Severity rate | 0.01 | 0.01 | 0.01 | 0.00 | 0.00 | |
Disasters involving deaths (Number of cases) | 0 | 0 | 0 | 0 | 0 |
Frequency rate: This is the total number of deaths and injuries due to industrial accidents per million cumulative actual hours worked, representing the frequency at which accidents occur
Severity rate: This is the total number of work-days lost per thousand cumulative actual hours worked, representing the degree of seriousness of accidents
*The figures are the results of Haseko Corporation’s construction sites on a non-consolidated basis (calculated including the employees of business partners).
*Average results for all industries and the general construction industry
for the frequency rate and severity rate are shown below.
(Fiscal year)
2018 2019 2020 2021 2022
・Frequency rate (One workday lost or more) Average for all industries1.83 1.80 1.95 2.09 2.06
Average for the general construction industry1.09 1.69 1.30 1.39 1.47
・Severity rate Average for all industries0.09 0.09 0.09 0.09 0.09
Average for the general construction industry0.30 0.29 0.24 0.41 0.22
Number of industrial accidents (number of disasters involving deaths)
This table can be scrolled
(Fiscal year) | 2018 | 2019 | 2020 | 2021 | 2022 |
---|---|---|---|---|---|
Haseko Group employees | 0 | 0 | 0 | 0 | 0 |
Employees of business partners | 1 | 0 | 0 | 0 | 0 |
*The figures are the results of the Haseko Group on a consolidated basis.
Promoting health
Basic approach to employees’ health
Since 2008, the Haseko Group has been providing support to its officers and employees for better physical and mental health by promoting "Healthy HASEKO Full-of-life Plan" under the slogan "No success without healthy officers and employees."
To describe its passion for and approach to health at the Group level, we released "Haseko Group’s Declaration of Health" in September 2017 and thereby presented our corporate policy for health to people inside and outside the Group.
Haseko Group’s Declaration of Health
We, at the Haseko Group, hereby make our declaration of health to pursue a group in which all employees—our most important business
resource—can maintain their health, both physically and mentally, and each and every one of them can work more vigorously, in order to fulfill our corporate philosophy "To contribute to society by creating an optimal environment for cities and people."
- Support for health
The Company will proactively work on maintaining and improving its employees’ health and provide support to them for better health. - Responsibility for health
Employees shall take responsibility for their own health and take action and make efforts accordingly on an ongoing basis. - For a healthy future
Our future must be unlocked by no one but ourselves. In order to open the way to Haseko Group’s future, let’s work together and make efforts as a team by giving top priority to our health.
Date of Establishment September 15, 2017
Haseko Corporation
President and Representative Director Kazuo Ikegami
Organizational framework for promoting health management
In accordance with Haseko Group’s Declaration of Health, we established the Haseko Group Health Management Promotion Committee in fiscal 2018. The Committee is chaired by the President of Haseko Corporation, its members are the respective officers in charge of departments of Haseko Corporation, the respective presidents of Group companies, industrial doctors, labor unions, and its secretariat consists of the Personnel Dept., the Safety Management Dept., the Welfare Dept. of Haseko Well Center, and the health insurance society. The Committee makes decisions on company-wide policies, targets, plans and progress related to the maintenance and promotion of employees’ health and shares related information.
Maintaining and enhancing health
Physical health
HASEKO CLINIC," an in-house medical office that serves as the health management and disease prevention center for Group employees, plays a pivotal role in our efforts for the early detection of diseases through medical checkups and outpatient treatment. The CLINIC has precision equipment comparable with hospitals and is capable of performing accurate and speedy tests.
The CLINIC not only conducts periodic medical checkups on all employees but also holds health seminars (e.g., improvement of diabetes, smoking cessation) andgives advice for the prevention of lifestyle-related diseases, in an e ort to enhance their health. Under the scheme for raising employees’ awareness of good health, certain employees are offered PET-CT scanning, while female employees are entitled to comprehensive women-only medical examinations.
Mental health
We have a structure in place to provide care to employees to maintain their mental health ranging from counseling to reinstatement assistance, including stress checks, as well as a structure to give support to employees in the event of the onset of mental illness.
Specific services available are: "self-care," which involves counselling and telephone consultation by a professional body outside the Group; "line care," which is a periodic training session held for managers to educate them and raise their awareness for the prevention of mental illnesses among their subordinates; and "reinstatement assistance program," in which a support team including an industrial doctor and the personnel division provides employees with full support at the Company level to return to work.
Refreshing
The Haseko Group believes that it is important for employees to have opportunities to expand their horizons in terms of hobbies and mates
and opportunities to refresh themselves, in order to maintain their physical and mental health. For this reason, we not only directly operate a recuperation facility but also introduce recuperation facilities and resort condominiums to employees and encourage employees to utilize them.
Furthermore, "Haseko Club" and "Everyone's Event," which are open to employees of the Haseko Group, provide the employees with opportunities to refresh themselves through physical exercise and cultural activities.
2024 Certified Health & Productivity Management Outstanding Organizations Recognition Program (White 500)
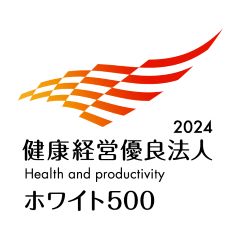
Haseko Corporation and its affiliates were recognized under the “2024 Certified Health & Productivity Management *Outstanding Organizations Recognition Program” in the large enterprise category hosted by the Ministry of Economy, Trade and Industry (METI) and Nippon Kenko Kaigi as one of the “organizations engaging in strategic health and productivity management program efforts for maintaining their employees’ health from a management perspective.”
*The term “health and productivity management” is a registered trademark of the Workshop for the Management of Health on Company and Employee.
Initiatives on labor issues
Support of living wage
Haseko Corporation conducts labor management in compliance with labor laws and regulations in each country and region. As for wages, we comply with minimum wage standards stipulated in each country and region, and pay higher wages than the standards as our basic policy. The average annual salary of the Corporation was 9.41 million yen in fiscal 2022.
Labor-management relationship
The Haseko Group has earned a labor-management relationship based on mutual trust between each Group company and the labor union of the Haseko Group. Aiming to realize a work-life balance for every union member and the development of the Group, the labor union collects voices from union members through questionnaires on their living and working conditions as well as meetings at worksites. Based on these voices, discussions and suggestions are made on equal footing through regular meetings between the employer and employees about developing a reassuring labor environment and measures for improving productivity. Each company takes these matters seriously to consider and implement various measures for the further development of the Group.
Risk assessment concerning labor issues
Each company in the Haseko Group monitors working hours as part of their employee work safety risk assessment, and reports the results to the Management Council on a monthly basis.
Based on the results of the monitoring, we take the following measures to ensure employee health and prevent overwork.
• We have formed “MOSt (Move on Steps) committees ” composed of labor and management personnel at each division of Haseko Corporation and within each Group company, to examine measures to reform operations, enhance productivity, and shorten working hours.
• We have established “Group-wide no overtime work hours day” (twice per year) and “division early finishing and going home early day” (once per month) as common measures across the whole Group.
• We apply overwork interview rules that are stricter than the statutory criteria.
We also monitor the status of employee health and promote initiatives to maintain and improve the health of our personnel through the “Haseko Group Health Management Promotion Committee.”
- Sustainability TOP
- Message from the Management
- Haseko Group's Sustainability Management
- D&I at the Haseko Group
- Climate Change Response
- Creating attractive living spaces
- Building a company worth working at
- Protecting the precious environment
- Nurturing a culture of trust
- ESG Data and Disclosures
- Integrated Report
- Philosophy and Policies
- Special feature archives