Protecting the precious environment
Cyclical resource use
We use resources carefully in every process of our business activities and aim to recycle them as much as possible.
Appropriate treatment and recycling status of construction waste
Construction waste treatment status
In fiscal 2022, the volume of construction waste discharged was 580,100 tons from new building construction work and 367,000 tons from demolition work, totaling 947,200 tons.
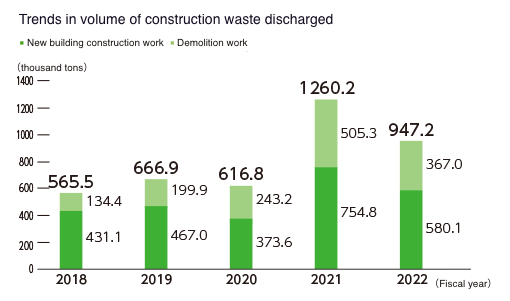
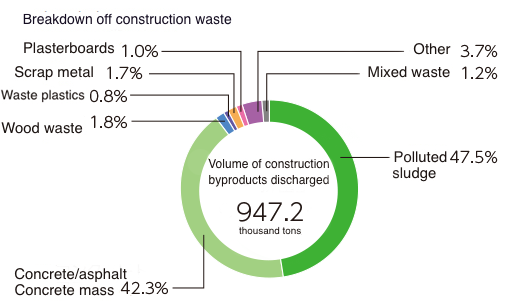
*The scope of coverage was reviewed in fiscal 2021 as follows.
- In and before fiscal 2020: Worksites completed during the fiscal year.
- Fiscal 2021 and after: Worksites in operation during the fiscal year.
Recycling status of construction waste
In fiscal 2022, the volume of recycled construction waste was 575,500 tons from new building construction work and 365,300 tons from demolition work, totaling 940,800 tons.
In demolition work, 1.50 tons of CFC refrigerants and 0.0 tons of halon were collected for destruction process and 1,503.0 tons of asbestos was properly processed and disposed of.
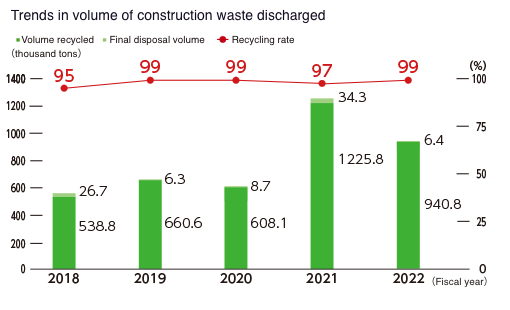
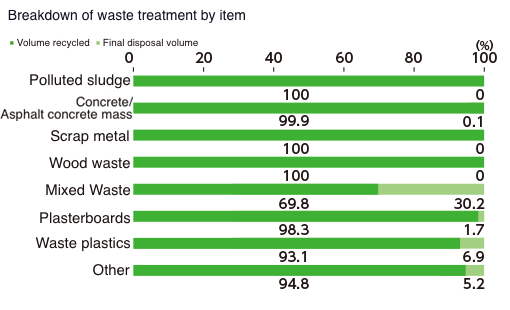
*The scope of coverage was reviewed in fiscal 2021 as follows.
- In and before fiscal 2020: Worksites completed during the fiscal year.
- Fiscal 2021 and after: Worksites in operation during the fiscal year.
Particle boards
We send waste wooden materials generated at construction sites to recycling facilities for recycling the waste into particle boards, and then use the particle boards manufactured from recycled waste at our construction sites. We thus engage in circular material recycling. This effort leads to the mitigation of environmental impact as the manufacturing process using recycled waste can reduce CO2 emissions, as compared with the manufacturing process using fresh wood, while it also contributes to conservation of forests.
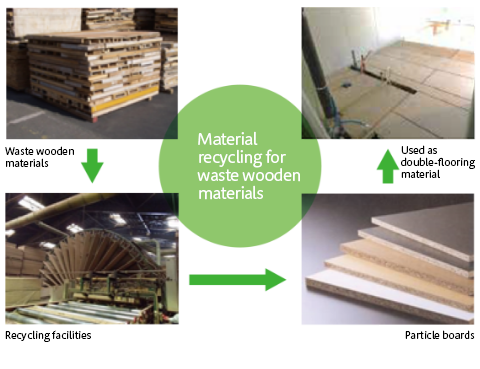
Promotion of recycling
The remnants of plasterboards generated at construction sites are recycled by plasterboard manufactures under the government-sponsored wide-area certification system, as well as by waste plasterboard recycling companies. The plasterboard waste is separated into plaster powder and paper, and then plaster powder is recycled into raw materials of plasterboards, while paper is recycled into raw materials for paper production. In fiscal 2022, we recycled 8,883 tons of waste plasterboards.
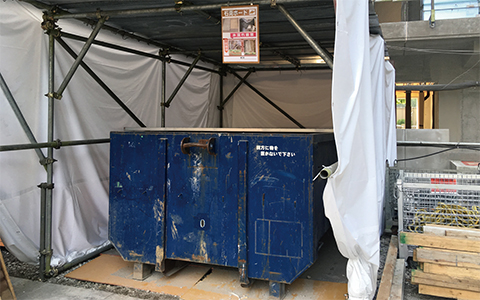
(protected from rain by roof and sheets)
Reduction of cardboard packaging materials by minimizing packaging and using returnable boxes
In order to reduce cardboard packaging materials at construction sites, we are working to minimize packaging and use returnable boxes for the transportation of materials and equipment related to facilities.
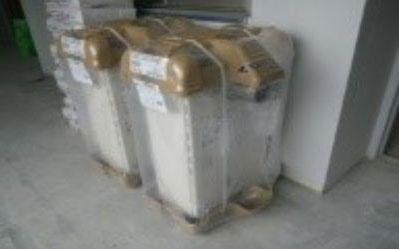
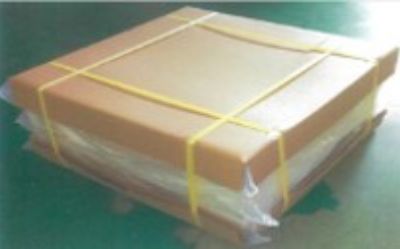
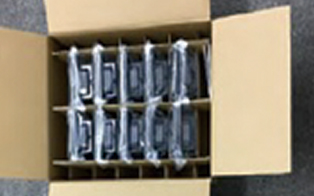
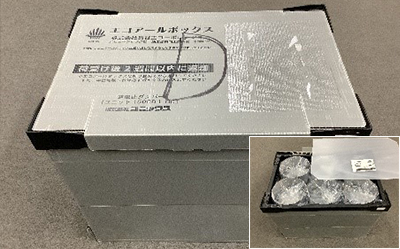
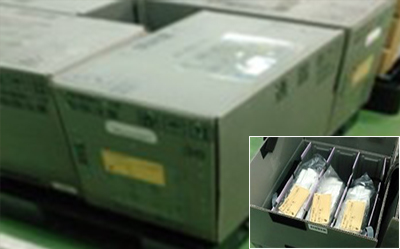
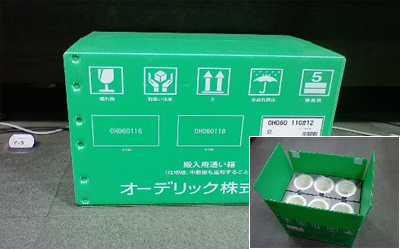
Execution division's educational initiatives
Education for new employees
In the fiscal 2022 training program for new recruits with an engineering background offered before assigning them to duties, we carried out a training session for sorting industrial waste at a construction site and a tour of an industrial waste intermediate processing facility. In the training program, new employees learned about the importance of sorting waste at the worksite through the tour of waste generation status and treatment process.

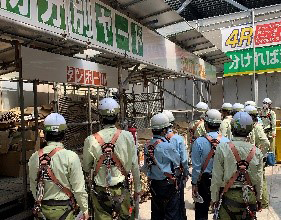
Education of skilled workers at construction sites
To promote the sorting and recycling of waste generated at construction sites, we have designated industrial waste disposal companies conduct a patrol to check the state of sorting at construction sites. Based on patrol results, we offer appropriate guidance on sorting for each site.
Several construction sites in the Kansai region have held ad hoc education sessions for the study of sorting industrial waste, etc. to enhance recognition and awareness on sorting items of industrial waste for a whole construction site. And they have conducted environmental patrols to check on the status of environmental related activities at each construction site and offered guidance as appropriate.
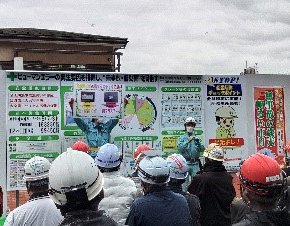
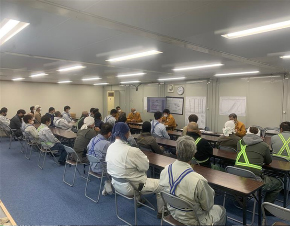
Initiatives to Reduce Wastes from Office Activities
Effective utilization of paper resources
In fiscal 2022, copy paper usage was 10.52 million sheets. Copy paper usage decreased 17.0% year-on-year by 2.15 million sheets. Going forward, we will continue to promote double-sided copying, copying of two or more pages on one side of paper, use of reverse side of used paper, and reduction of conference materials in an effort to effectively utilize paper resources.
*Shiba Head Office Building/Osaka Hiranomachi Building/Yokohama Branch/Nagoya Branch/Haseko Technical Center
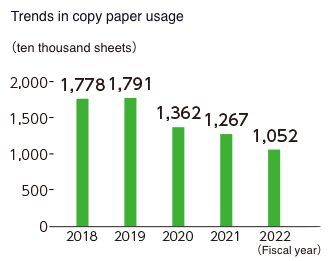
Reduction of total waste disposal volume
The total waste disposal volume in fiscal 2022 increased 10.4% year-on-year to 14.9t. Going forward, we will continue making efforts to reduce the volume of waste by utilizing recycle boxes and separating waste in thoroughgoing manner.
*Shiba Head Office Building/Osaka Hiranomachi Building
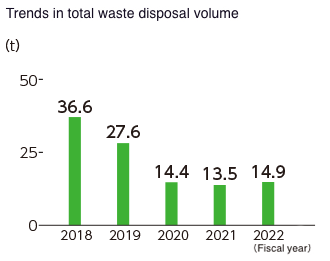
Water resources
Water is an essential resource for people's lives. In order to carefully use limited water resources , the Company monitors its water usage and prevents pollution, striving to reduce water usage and conserve water resources.
Water Usage Trends
The Company's water usage is as follows.
Category | Unit | FY2018 | FY2019 | FY2020 | FY2021 | FY2022 | |
---|---|---|---|---|---|---|---|
Total water intake*1 | Construction sites | ||||||
Water intake | thousand m3 | 349 | 408 | 387 | 950 | 660 | |
Office activities | |||||||
Water intake | thousand m3 | 30 | 28 | 21 | 25 | 25 | |
Total water usage | thousand m3 | 379 | 435 | 408 | 975 | 685 | |
Total effluents*2 | Construction sites | ||||||
Effluents | thousand m3 | 295 | 308 | 20,927 | 377 | 739 | |
Office activities | |||||||
Effluents | thousand m3 | 28 | 26 | 19 | 23 | 23 | |
Total effluents | thousand m3 | 323 | 333 | 20,946 | 400 | 762 |
*1. Aggregated amount of water taken from public water. Does not include intake from surface water, subsurface water, marine water, or external effluent.Total effluents
*2. Aggregated amount of water discharged to public water. Does not include discharge to surface water, subsurface water, or marine water.
Adoption of water-saving equipment in Haseko condominiums
Haseko Corporation and Haseko Property Management Holdings have developed the Smart Water Tank, which collects and stores rainwater from condominium roofs. The stored rainwater can be used efficiently for watering plants, enabling preservation of water resources. Additionally, when combined with the WELLUP proprietary emergency water purification system, drinking water is supplied to residents in emergency situations. Along with increased adoption in the Group’s for-sale condominiums, the technology is gradually being installed in condominiums with 200 or more units designed and constructed by Haseko Corporation.
As part of our green procurement initiatives for construction materials, we are promoting installation of water-saving toilet bowls (please refer to “Green procurement initiatives” for numbers of water-saving toilet bowls installed).
- Related information
Business activities in water-stressed areas
Japan is the key location for Haseko Corporation’s business activities. In the World Resources Institute’s “Aqueduct 4.0” report, Japan’s water stress is rated low-medium, indicating it is an area of relatively little water stress. As of the end of September 2023, our business activities overseas are limited, but if in the future we expand our business into regions where water stress is a concern, we will engage in proper management.
- Sustainability TOP
- Message from the Management
- Haseko Group's Sustainability Management
- D&I at the Haseko Group
- Climate Change Response
- Creating attractive living spaces
- Building a company worth working at
- Protecting the precious environment
- Nurturing a culture of trust
- ESG Data and Disclosures
- Integrated Report
- Philosophy and Policies
- Special feature archives